川十のデジタル活用・DX推進 Digital technology and DX promotion
川十でのデジタル活用・DX推進の取組みをご紹介いたします。
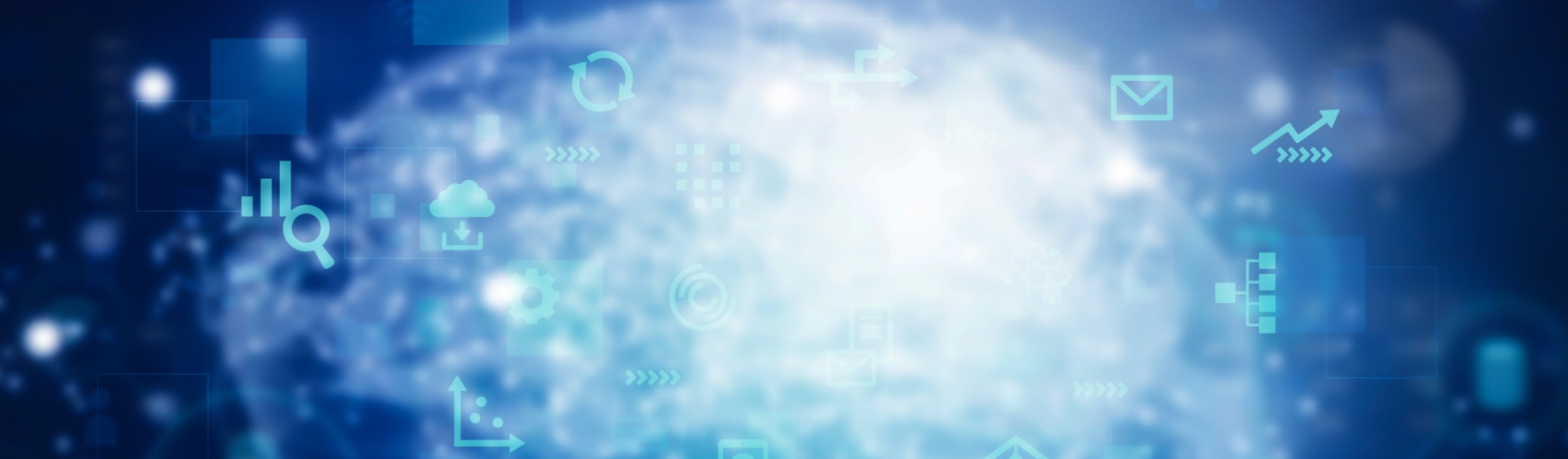
デジタル技術の活用で生産性を向上
川十では、製造現場の業務をデジタル化することで、生産性を向上させ、多品種少量の超短納期生産への最適化を図っています。

デジタル技術等の導入背景
川十では、デジタル技術を活用し、生産管理システムを確立することで、当社の強みのコアである多品種少量の超短納期生産への最適化を計り、今後増加していくジャストインタイム生産システムを導入する顧客への売上拡大を図ります。
製品の安定供給体制の構築
- 20%の生産性向上とコストの削減を見込む
- 顧客の望む短納期対応や高品質・安定供給を行うことが可能
- 自動化により低感染リスク型の生産プロセスを構築
属人的な管理から脱却し、新型コロナウイルスの感染拡大及びポストコロナの状況に対応したビジネスモデルへの転換
価格的優位性
- 設備の見える化と製造順序の最適化生産の実現により、生産完全受注生産による多品種少量生産と顧客へのジャストインタイムが実現
- トレーサビリティ―の提供により価格以上の優位性を提供
性能的優位性
- 最適生産の実現により、属人化解消により品質向上に寄与
- シミュレーション機能により、目的とする加工に最適な設備と加工方法を設定できることにより加工精度の高い製品を提供
デジタルツインで業務を効率化
外部事業者と連携して新たにシステムを開発し、「生産状況の見える化」と「シミュレーションによる生産計画の最適化」のシステムを導入。
またデジタルツインの取り組みにより、
①オペレーションへの活用として、「見える化」による現場作業の効率化を図っています。
②「シミュレーションへの活用」として、人員配置、投入計画、設備配台計画による生産効率の改善を図っています。
生産状況の見える化
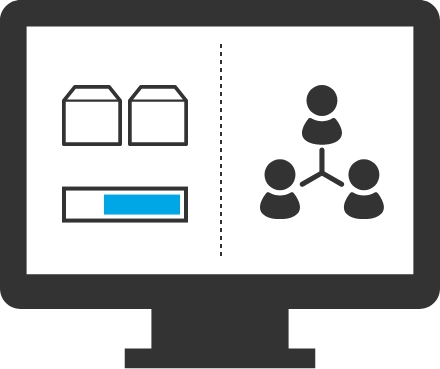
シミュレーションによる
生産計画の最適化
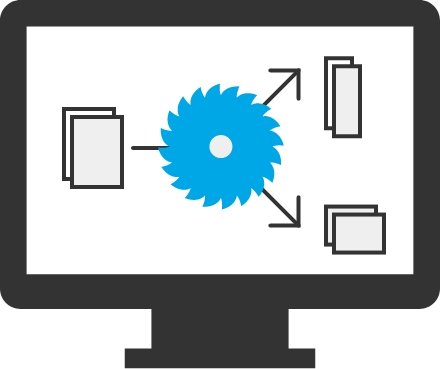
デジタル技術の活用プロセス
業務プロセスの改善
スマート化の目的
業務最適化を図り、生産性を向上させる
[レベル1]データの収集・蓄積
- 作業量を計るため、各種ビッグデータを収集。(材料切断速度等)
- データベースとして各種データを蓄積する。
[レベル2]データの分析・予測
- 収集したデータを元に各作業工程のスループットを出す。
- スループットを整理し各作業工程のボトルネックを見える化する。
[レベル3]データによる最適化
各工程のスループットや各種データをもとにシミュレーションツールを用い製品設計を自動化し、業務最適化を図る。
システム構築の流れ
全体設計
- 要件定義
- サーバーの構築
- コード定義
- 機能一覧表作成
- 業務フロー図作成
- 入出力関連図作成
- 画面設計書作成
各種機能設計
- TOPページ構築
- 受発注管理連携構築
- 在庫管理機能構築
- データ収集機能構築
- シミュレーションツール構築
- 各種データ出力機能
デザイン設計
- 画面イメージ
- 色や配置
- 動き方
- UI(動線)設計
テスト運用・改修
- 動作テスト
- エラー解析
- 各種エラー改修
全体のシステム構成イメージ
既存システムを活用して、IOTで現場情報を収集し、現場データの見える化を行っています。 さらに、オーダー情報と作業データ、現場情報を統合して、生産シミュレーションにより、製造順序を最適化し、投入計画、人員配置の立案・修正を自動化。これらを外部事業者のパッケージソフトを活用することでシステム構築期間を短縮し安価に構築するとともに、自社による改修を可能にします。
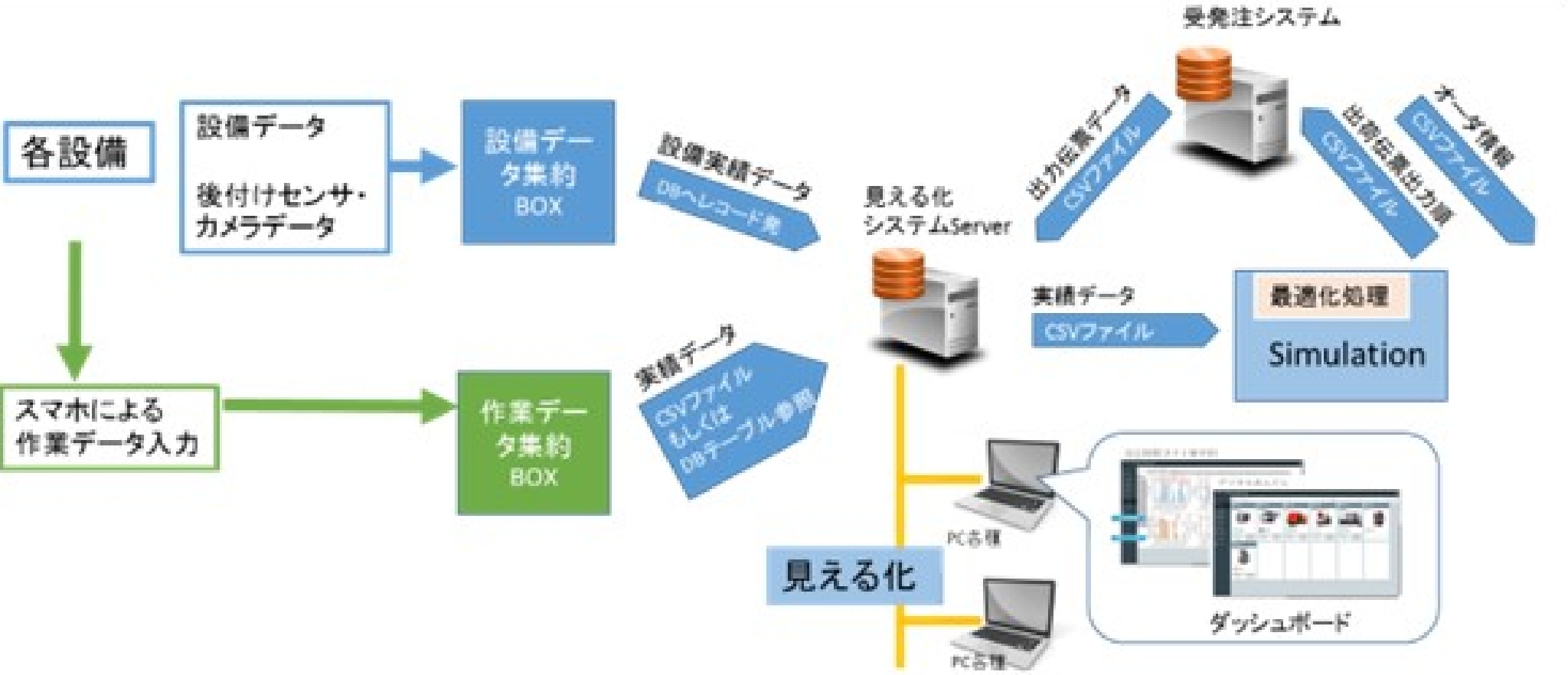
①業務可視化におけるデータ収集システム導入
製造プロセスにおけるスループットの改善のため、既存システムを活用して、スマホ入力による作業データや運転、停止、異常、速度などのデータを各設備から、自動でデータ収集を行います。レガシー設備をIOT化するために、後付けのセンサとカメラのOCRの技術を活用。受発注システムとのデータ連携により、受注入力、納品書作成なども自動化しています。
②スループットの見える化
取得したデータを作業ごとに整理を行い、どの製品がどれくらいのスループットなのか、ボトルネックを見える化します。専門知識が無くても構築できるDB(DrSUM)で様々なデータを加工・集約。ノンプログラミングで設計可能なBIツール(Motion Board)でモニタ表示します。
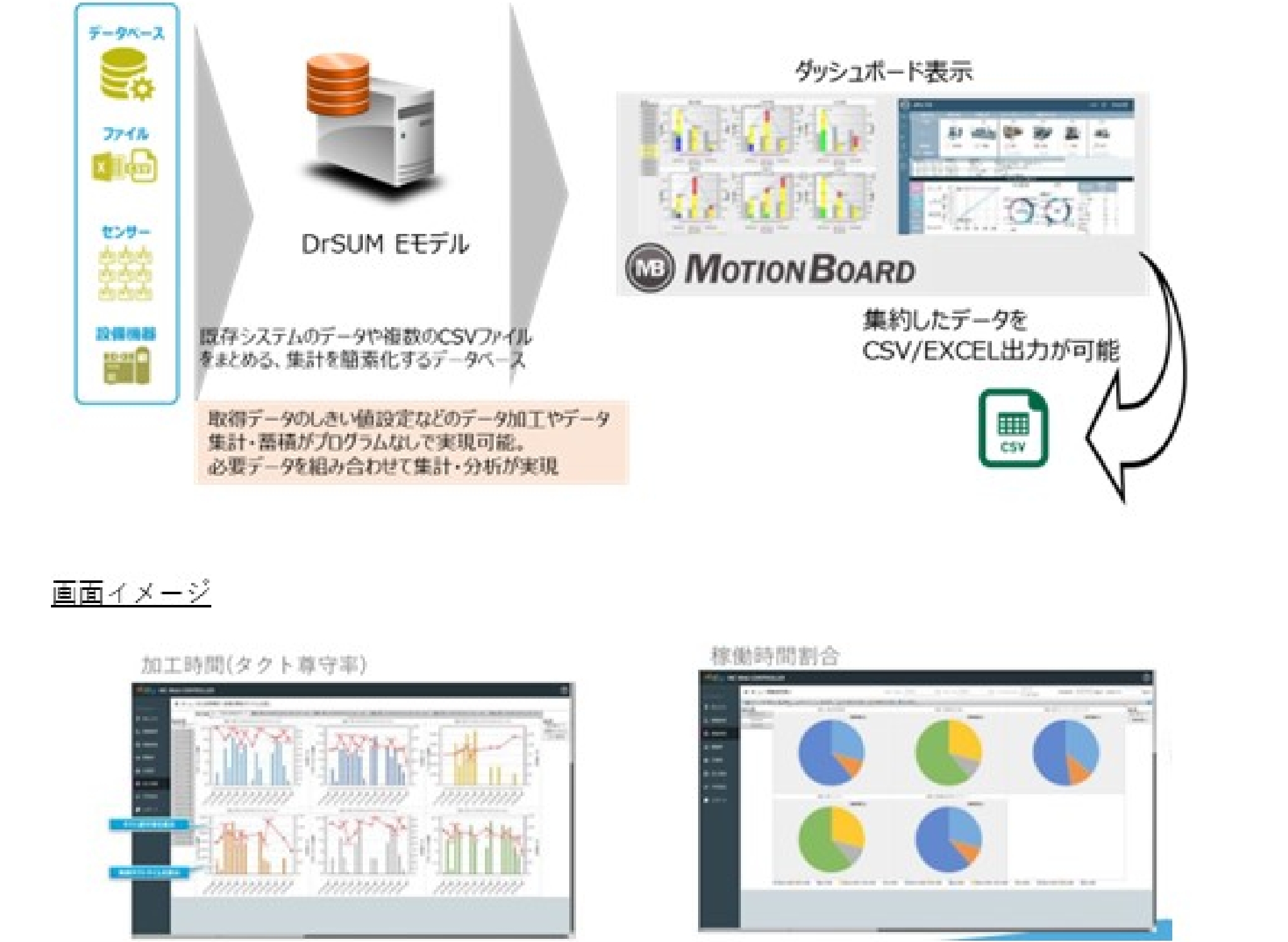
③シミュレーションにおける製造順序の最適化
受注順で製造するのではなく、段取り・在庫量・加工時間、設備の稼働状況からどの順番で加工・製造するのが一番効率的か、シミュレーションツールを活用し製造順序を最適化。材料在庫の最適化にも活用できます。
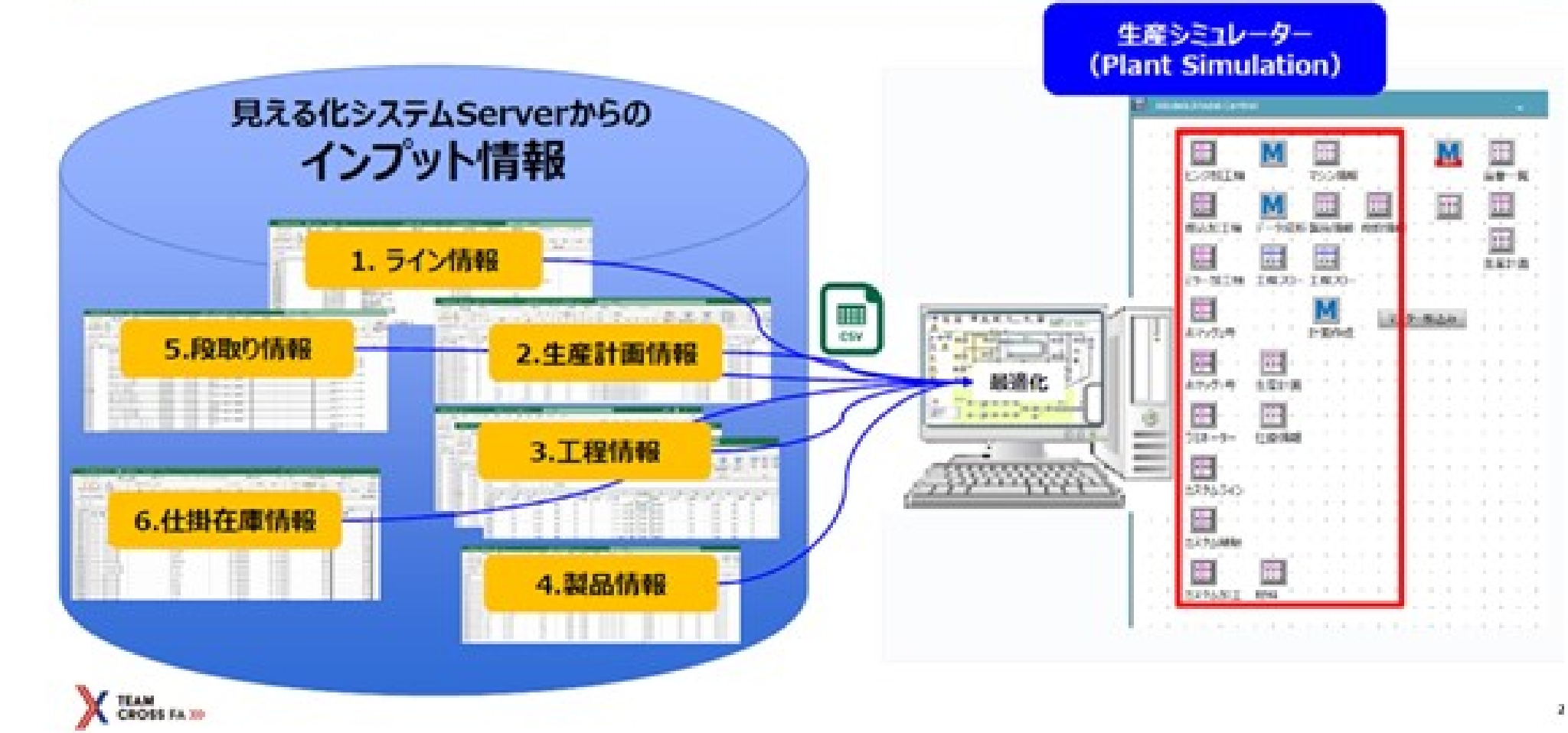
デジタルツインによるシミュレーションの運用イメージ
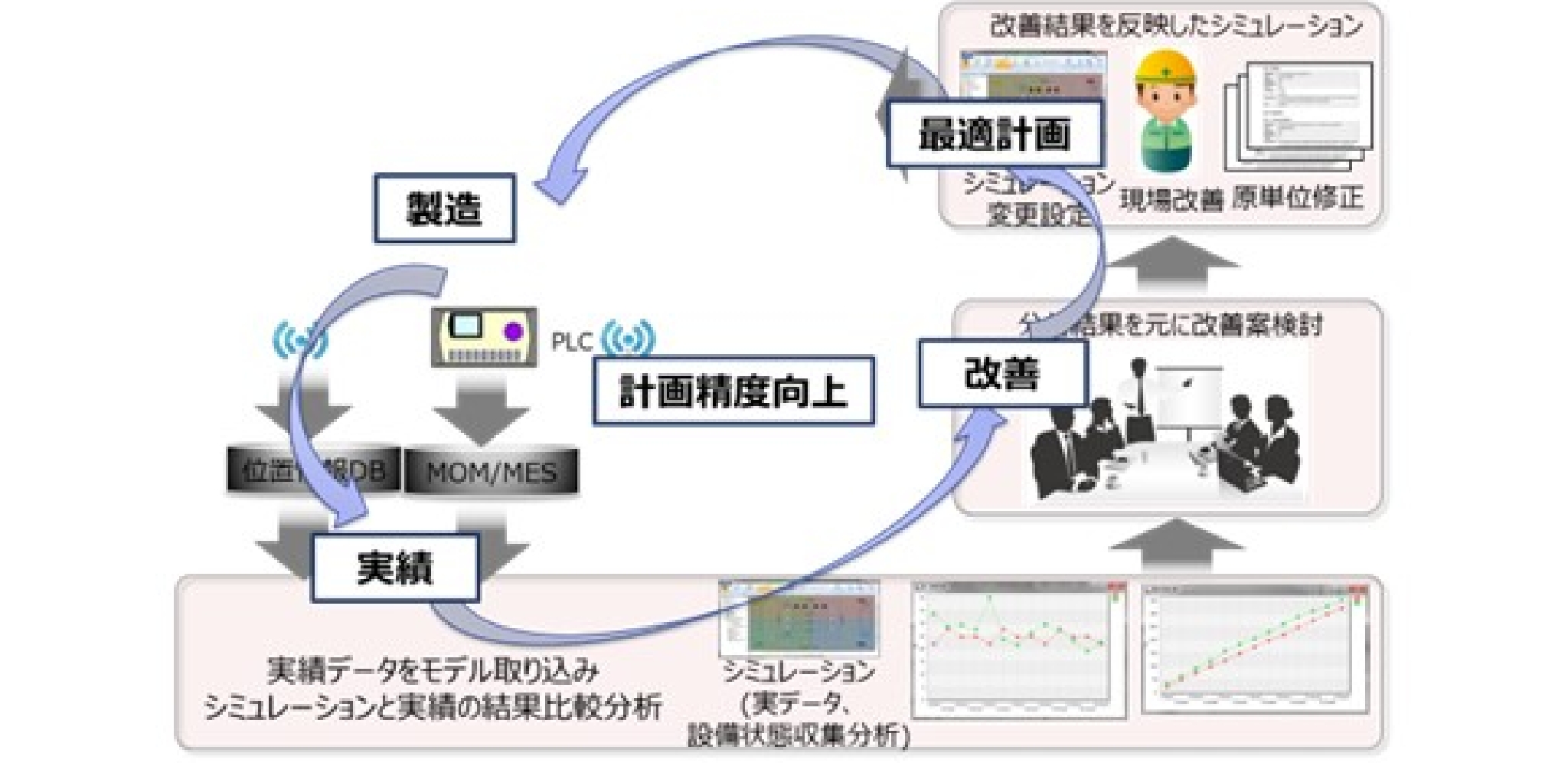
配送業務のデジタル化
川十では、配送業務をデジタル化し、業務効率化を図っています。
積荷チェックは、新しく以下の二種類になります。
①送り状無し:現品票のみの積荷チェック
②送り状有り:送り状+現品票での積荷チェック
現場のiPod touchのメニューに、送り状無し用、送り状有り用、それぞれの積荷チェックの画面を用意します。
送り状無しと有りのどちらの画面で処理をするのかは、伝票の取引先ごとで決定します。
配達順データの「積荷送り状有無」で管理しています。
積荷チェック
①送り状無し用の積荷チェック画面:伝票の取引先が配達順データの「積荷送り状有無」の設定されている伝票しか処理できない
②送り状有り用の積荷チェック画面:伝票の取引先が配達順データの「積荷送り状有無」の設定されている伝票しか処理できない
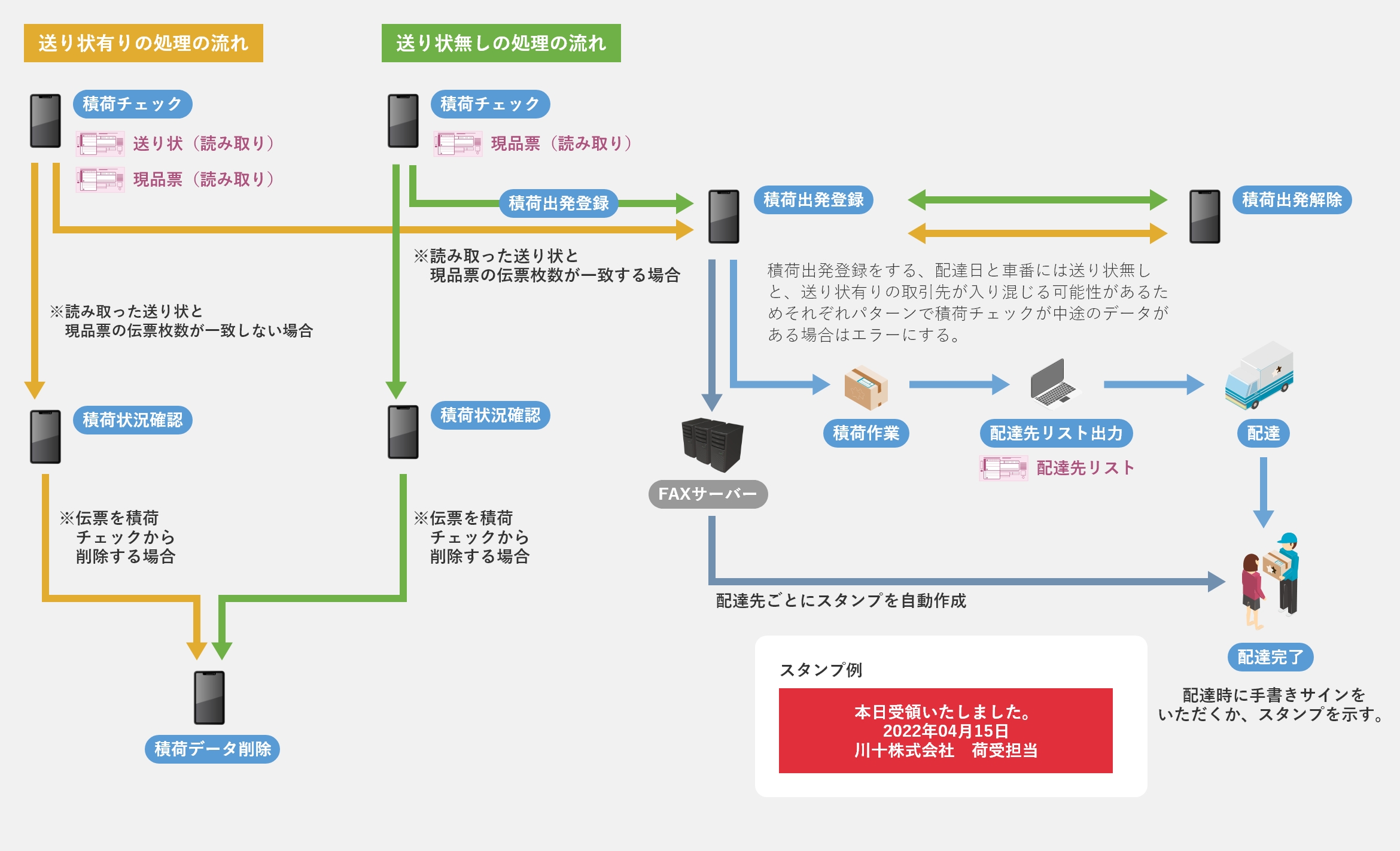
社内実施体制
実施のための社内体制と役割
本事業は当社において非常に重要な位置づけとなっているため、代表取締役:亥子勝高をリーダーとするプロジェクトチームを立ち上げ、全社体制で取り組みを行っています。課題解決に係る技術習得並びに生産体制の確立は、当社の強みである生産管理システムを使い、実施責任者及び現場責任者が中心となって会社全体で実施します。
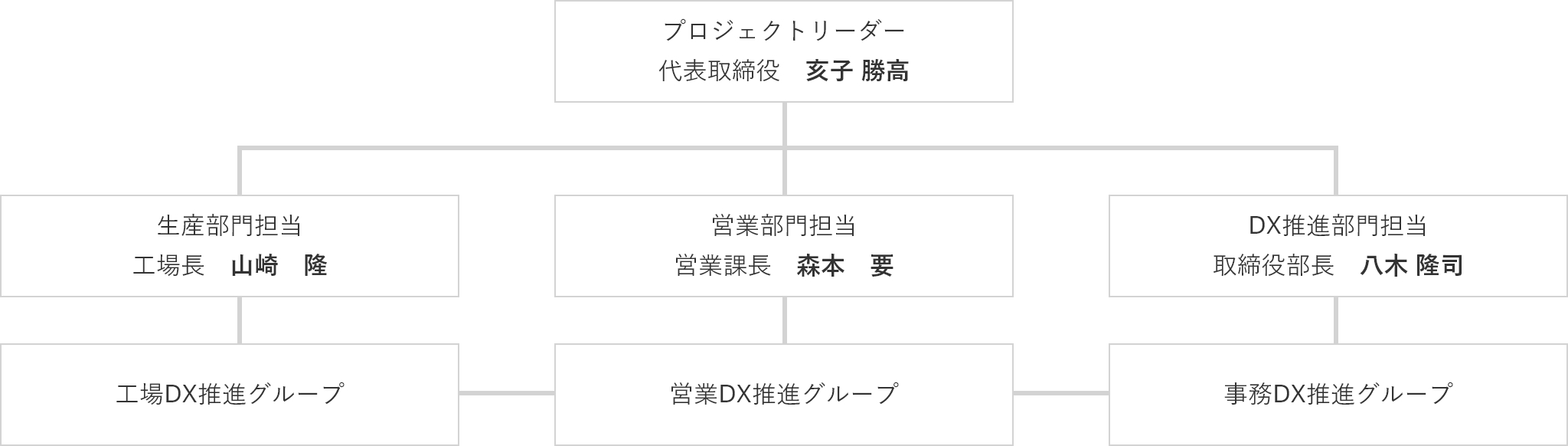